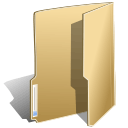
硬质合金刀具 (204)
硬质合金涂层刀具工艺灵活化
- 星期五, 06 12月 2013 08:06
- 作者 硬质合金产品编辑2
硬质合金涂层刀具的单一涂层无法满足切削加工中越来越复杂要求,因此,便出现了涂层多样化的工艺组合。“渗氮/PVD”复合涂层技术就是其中的一种。早在1983年就有人提出等离子氮化与离子镀工艺结合起来。通过基体的热化学预处理来提高硬质防护涂层性能的技术越来越受到关注。对基体进行渗氮和离子镀TiN复合处理后,可形成一个合理的硬度梯度分布,而在沉积过程中又由于TiN与N的作用及向渗氮层内部进一步扩散,使过渡层的硬度比单一渗氮层要高100HV0.1左右,从而使复合涂层得到强化。更多信息,请访问:硬质合金刀具。 将化学气相沉积与物理气相沉积的工艺进行组合是硬质合金刀具涂层工艺多样化的一个重要的发展方向,新型涂层利用了化学气相沉积与物理气相沉积相结合的方法,起始层是由CVD形成的TiN,目的是提高涂层与基体的结合强度,中间层是CVD的TiCN,外层是PVD的Ti系特殊膜,使其具有较好的耐热性即提高刀具刃口的锋利性。因为残余应力在CVD层是拉应力,在PVD层是压应力,其结果是提高了涂层刀具的抗热震性能。 硬质合金涂层刀具的涂层以及发展到在基体涂10层、甚至更多层,每层厚度越来越薄,硬质合金刀片质量越来越好。利用多层膜具有的界面效应和层间耦合效应以及裂纹尖端钝化、裂纹分支及沿界面的界面开裂等增韧机制来提高多层涂层的韧性,从而获得与单层涂层不同的特性。更多信息,请访问:http://www.tungsten-carbide.com.cn/Chinese/carbide-cutting-tools.html
发布于
硬质合金刀具
硬质合金涂层刀具介绍
- 星期五, 06 12月 2013 08:04
- 作者 硬质合金产品编辑2
硬质合金涂层刀具就是在硬质合金刀具基体上涂上一层或多层硬度高、耐磨性好的金属或非金属化合物薄膜的涂层刀具,结合了基体高强度、高韧性和涂层高硬度、高耐磨性的优点,降低了刀具与工件之间的摩擦因数,提高了刀具的耐磨性而不降低基体的韧性。因此,涂层硬质合金具有高硬度和优良的耐磨性,延长了刀具的寿命。涂层刀具后处理技术对刀具性能有一定的影响,硬质合金涂层刀具后处理技术包括热处理、磁化处理,深冷处理,随着技术的进步,更多更新型的后处理技术将带来涂层刀具的又一次变革。更多信息,请访问:硬质合金刀具。 硬质合金涂层刀具的涂层方法在不停的完善,越来越复杂化和多样化。从最初的高温化学气相沉积涂层发展为等离子化学气相沉积涂层、中温化学气相沉积涂层和离子辅助物理气相沉积涂层等。目前硬质合金刀具涂层方法的发展方向是物理气相沉积。 硬质合金涂层刀具的涂层种类也在不停的完善,从单一的化合物涂层朝着多元复杂化合物涂层发展;涂层层数也从几层到十几层;新型的涂层基体也在不断推出,具有梯度结构的硬质合金涂层基体使硬质合金涂层刀具性能进一步得到提高;涂层工艺方法不仅不断更新换代,而且实现了多种工艺的灵活组合,以得到高性能的刀具涂层。更多信息,请访问:http://www.tungsten-carbide.com.cn/Chinese/carbide-cutting-tools.html
发布于
硬质合金刀具
硬质合金涂层刀具成分多元化
- 星期五, 06 12月 2013 08:02
- 作者 硬质合金产品编辑2
随着科技的不断发展,硬质合金涂层刀具的单元涂层已经不能满足市场的需求,于单元涂层刀具的基材与涂层材料的硬度、弹性模量及热膨胀系数不匹配,晶格类型也不一样,致使基体与涂层之间产生残余应力,结合力不强。在单涂层中加入新的元素(如加入Al、Cr和Y提高抗氧化性,加入Zr、V、B和Hf提高抗磨损性,加入Si提高硬度和抗化学扩散)制备出多元的刀具涂层材料,大大提高了硬质合金涂层刀具的综合性能。在多元硬质合金涂层刀具中,最常用的则是TiCN、(Ti,Al)N涂层。更多信息,请访问:硬质合金刀具。 硬质合金涂层刀具中的TiCN涂层兼有TiC和TiN涂层的良好韧性和硬度,它在涂覆过程中可通过连续改变C和N的成份来控制TiCN的性质,并可形成不同成份的梯度结构,降低涂层的内应力,提高韧性,增加涂层厚度,阻止裂纹扩展,减少崩刃。随着中温化学气相沉积(MT-CVD)新技术的出现,使CVD技术发生了革命性变革。MT-CVD技术是以有机物乙腈(CH3CN)作为主要反应气体,在700℃以下生成TiCN涂层。这种TiCN涂层方法有效控制了很脆的η相(Co3W3C)生成,提高了涂层的耐磨性、抗热震性及韧性。在PVD沉积TiCN涂层时适当增加离子束轰击也可明显提高涂层的硬度及耐磨性。近年来,以TiCN为基的四元成分新涂层材料(如TiZrCN、TiAlCN、TiSiCN等)也纷纷出现。 (Ti,Al)N涂层材料是目前应用最广泛的硬质合金刀具涂层之一,(Ti,Al)N有极高的高温硬度和抗氧化能力,最高工作温度800℃,氧化起始温度700℃,涂层硬度HV3000,颜色为紫灰色。(Ti,Al)N涂层比TiN更能有效地用于连续高速车削,也适合于加工铁合金、镍合金不锈钢等工件。这种涂层因固溶硬化而有较好的硬度保持性,其抗氧化性能也比TiN和TiCN强。TiAlN在切削时会在刀屑界面上生成一种非晶体的氧化铝,形成一层硬的、惰性的保护膜,此膜的导热性差,可使切削热更多地由切屑带走。高速干式切削最好的涂层是氮铝化钛(TiAlN),涂层的作用就象一层热屏障,因为它有比刀具基体和工件材料低得多的热传导系数,在高温连续切削时,TiAlN高速干式切削优于TiN四倍。更多信息,请访问:http://www.tungsten-carbide.com.cn/Chinese/carbide-cutting-tools.html
发布于
硬质合金刀具
硬质合金刀具钻削切屑控制
- 星期五, 06 12月 2013 08:02
- 作者 硬质合金产品编辑2
硬质合金刀具钻削切屑控制和切削液是钻削中的关键所在,生成合适的钻削切屑形状和大小以及排除它们对任何钻削工序都是至关重要的。在这种情况下,如果没有满意的性能,任何钻头都会由于硬质合金刀具钻削切屑会在孔内堵塞而在短时间内停止切削。现代钻头高切削速度和高进给都可以通过使用切削液在获得有效的排屑时变为可能。硬质合金刀具钻削过程中的切削液是一种用在金属切削、磨加工过程中,用来冷却和润滑刀具和加工件的工业用液体,切削液是由多种超强功能助剂经科学复合配伍而成。更多信息,请访问:硬质合金刀具。 硬质合金刀具钻削过程中,钻削切屑的形成会因为工件材料、刀具槽形、切削速度、进给和一定程度上切削液选择而受到影响。一般来说,高进给、低切削速度将产生短的钻削切屑。如果钻削切屑可以稳定地流出,钻削切屑长度和形状就可以说是可接受的。大部分浅孔钻有两个排屑槽。使用现代机床和钻削刀具时,通过钻头内冷却液孔提供切削液,可以有效地完成排屑。切削时,切削液从钻头的顶尖喷射出,不但可以润滑钻头,而且切削液使钻削切屑通过排屑槽流出。 现代硬质合金钻头具有高金属去除率和大密度的排屑槽。在高压下,通过内供式切削液将这些钻削切屑排出。所需的压力(Mpa)和流量(升/分)主要取决于孔径,但是也受到切削条件和工件材料的影响。 硬质合金刀具钻削过程中,当切削液通过内部进行供应的时候,因为离心力的影响,将引起压力降低,旋转钻比非旋转钻要求更高的切削液压力。这并不必须用很高的切削液压力来补偿,可以使用流量补偿器。但是,对于非旋转钻和使用外切削液,也需考虑传输系统内压力的下降。更多信息,请访问:http://www.tungsten-carbide.com.cn/Chinese/carbide-cutting-tools.html
发布于
硬质合金刀具
硬质合金刀具的磨损机理
- 星期五, 06 12月 2013 08:00
- 作者 硬质合金产品编辑2
在硬质合金刀具磨损的开始阶段,粘结相Co发生塑性变形,表层的Co被WC晶粒挤出。由于Co的硬度小、延展性好,在某些条件下,可在表面形成微米级的摩擦膜,同时较硬的WC颗粒则慢慢突出于摩擦表面,避免了表面进一步迅速磨损,摩擦过程进入相对稳定的阶段。随着粘结相Co的不断流失,材料的WC骨架遭到破坏,WC颗粒内部位错密度显著增加,当位错密度积累到一定量时,就会在WC颗粒上形成微裂纹,进而使WC颗粒开始从硬质合金刀具基体中拔出。脱落的WC颗粒留在磨损区内,转变成磨粒,在载荷的作用下与基体发生挤压,从而产生新的塑性变形和晶粒的破损。更多信息,请访问:硬质合金刀具。 随着硬质合金刀具晶粒的减小,晶粒致密度增加,表面磨损程度下降。WC晶粒脱落现象,通过EDS分析也可以证明。ZHX硬质合金刀具的表面WC颗粒的脱落不明显,而HG表面致密度非常好,几乎没有明显的WC颗粒的脱落。因此,对于传统晶粒尺寸的硬质合金刀具ZH,主要的磨损机理为粘结相Co的挤出和WC晶粒的脱落而造成的磨粒磨损,而随着晶粒尺寸的减小,细晶粒硬质合金刀具致密度的增加,WC晶粒的剥落现象减小,Co依旧包裹在WC的周围,材料的微观结构还保持完整,大多数晶粒只产生了一定的塑性变形。更多信息,请访问:http://www.tungsten-carbide.com.cn/Chinese/carbide-cutting-tools.html
发布于
硬质合金刀具
硬质合金刀具摩擦过程
- 星期五, 06 12月 2013 07:59
- 作者 硬质合金产品编辑2
在每个硬质合金刀具摩擦过程都遵循类似的规律,即初期动摩擦因数都经历一个从初始值迅速增大的过渡期,而后保持相对稳定,且在平稳阶段呈现波动特性。开始阶段,在法向载荷作用下,摩擦表面只有局部微凸体接触,黏着面积较小,接触表面的分子引力较小,所以摩擦系数较小;随着摩擦过程的进行,微凸体发生干涉,逐渐被磨平,黏着面积逐渐增大,分子引力也在增大,导致摩擦系数逐渐增大。整个硬质合金刀具摩擦过程就是接触表面不断地黏着,而后在切应力作用下又不断地剪断的过程。由于表面Co相的剥落、破碎而引起试样表面的磨损,表面的局部黏着很快达到一个动态平衡,从而导致表面的摩擦系数维持在较稳定的范围内,称之为稳定期。更多信息,请访问:硬质合金刀具。 大多数都将一段时间(距离)内的摩擦系数的平均值作为摩擦行为的表征参量。因此,选取在稳定摩擦阶段的平均值作为在相应参数下硬质合金刀具的摩擦系数。可见,随着摩擦速度和载荷的提高,硬质合金刀具的摩擦系数整体上呈现下降的趋势,同时在相对低速(40m/min与80m/min)与高速(120m/min与160m/min)的过渡部分下降最为明显。 从材料的角度看,ZH硬质合金刀具的摩擦系数小于其他两种材料,ZHX与10工具技术可见,随着摩擦速度和载荷的提高,硬质合金刀具的摩擦系数整体上呈现下降的趋势,同时在相对低速(40m/min与80m/min)与高速(120m/min与160m/min)的过渡部分下降最为明显。从材料的角度看,ZH硬质合金刀具的摩擦系数小于其他两种材料,ZHX与10工具技术HG两种硬质合金刀具的摩擦系数相差不大,其中HG硬质合金刀具的摩擦系数略大。更多信息,请访问:http://www.tungsten-carbide.com.cn/Chinese/carbide-cutting-tools.html
发布于
硬质合金刀具
硬质合金刀具钻削的切削力
- 星期四, 05 12月 2013 09:56
- 作者 硬质合金产品编辑2
当硬质合金钻头穿过产品去除不需要的金属时,硬质合金刀具钻削切削力作用在硬质合金钻头上,所以对于硬质合金刀具钻削有一定钻削功率的要求。钻削功率除了材料因素外,钻削功率(Pc)还与直径、进给率和切削速度有关。所需近似钻削功率的计算公式可以用来检查机床能否满足钻削功率的需要。对于现代机床来说,硬质合金刀具的钻削大部分中等直径的孔是没有问题的,但是对于有几倍孔径深度的大直径孔来说,还是需要检查钻削功率。更多信息,请访问:硬质合金刀具。 对于大直径硬质合金刀具的钻削工序来说,特别是对于套孔考虑在切削时钻头所承受的总钻削扭矩时,以纳米为单位的扭矩值是另一个有效值。进给、直径、材料是影响扭矩值的主要因素。扭矩是在每个切削刃上的扭矩的总和,是切向力和半径到中心距离的径的乘积。 硬质合金刀具钻削加工中的进给力,以N为单位的进给力(Fƒ)是最重要的因素。这是穿透材料时作用在钻头上的轴向力。因为确保主轴钻削功率和主轴强度满足钻削工序的要求是非常重要的,因此需要考虑过大的进给力会影响到孔的质量、钻头的可靠性和使机床停转。在另一方面,从生产率的观点来看,足够的进给力对钻削作用是重要的。进给力和钻头的直径、进给和所切削的材料有关。钻头的切削刃角度(kr)也会影响进给力。更多信息,请访问:http://www.tungsten-carbide.com.cn/Chinese/carbide-cutting-tools.html
发布于
硬质合金刀具
硬质合金刀具钻削的切削参数
- 星期四, 05 12月 2013 09:55
- 作者 硬质合金产品编辑2
硬质合金刀具钻削切削参数是指切削速度、每转进给、穿透率或进给速度和孔深四个参数。切削速度是刀具切削刃上的某一点相对于待加工表面在主运动方向上的瞬时速度。从孔加工的观点来看,可表示孔特性的主要因素包含:直径、深度、质量、材料、加工条件或工况、可靠性、生产率。硬质合金刀具钻削加工是根据硬质合金钻头或者扩孔钻在钻床上进行加工模具零件孔的方法,钻削刀具与工件作相对运动并轴向进给运动。更多信息,请访问:硬质合金刀具。 硬质合金刀具钻削加工切削参数中的切削速度,一般用字母VC表示,单位为m/min,是由圆周速度确定的,切削速度可以用主轴转速计算(n)得到。主轴转速是以每分钟转数表示的。在一转中,钻头周长为π×Dc,Dc为钻头直径。钻削加工切削参数中的切削速度会发生变化,它取决于钻头上切削刃的横截面。从钻头中心到圆周,其速度从零到最大值。推荐的切削速度为圆周的最高速度。 硬质合金刀具钻削加工切削参数中的每转进给,一般用ƒn表示,单位为mm/min,表示了在一转中刀具的轴向运动。它用于计算穿透率,和用于表示钻头的进给能力。 硬质合金刀具钻削加工切削参数中的穿透率或进给速度,一般用字母Vƒ表示,单位为mm/min,是刀具相对工件的进给,它用长度/单位时间表示,也叫机床进给或工作台进给。每转进给与主轴转速的乘积给出了钻头穿透工件的速率。 硬质合金刀具钻削加工切削参数中的孔深,一般用字母L表示,是用于计算的一个重要因素。更多信息,请访问:http://www.tungsten-carbide.com.cn/Chinese/carbide-cutting-tools.html
发布于
硬质合金刀具
硬质合金刀具铣削问题
- 星期四, 05 12月 2013 09:54
- 作者 硬质合金产品编辑2
硬质合金刀具铣削的时候,当铣削时振动过大,可能发生的问题有装夹较差、工件不牢固、使用了大悬伸刀具、用不稳定主轴铣削方肩和工作台进给不规则等。当铣削表面质量差时,可能发生的问题有铣削每转进给量过大、铣削振动、铣削刀片上形成积屑瘤、反向铣削和工件崩碎等。当硬质合金刀具常规铣削时刀片崩裂,可能导致刀片退出时切屑厚度过大。当硬质合金刀具方肩铣削时刀片崩裂,就会发生逆铣铣削时切屑附着刀片,使方肩和铣削刃之间粘连、顺铣铣削需多次走刀、铣削切屑堵塞在方肩和切削刃之间等问题。更多信息,请访问:硬质合金刀具。 硬质合金刀具铣削时如果振动过大,导致装夹较差的时候,解决方法有:评估切削力和支撑方向或改善装夹;通过减小铣削切削深度来降低铣削切削力;选择疏齿和不同齿距的铣削铣刀可获得更积极的切削作用;选择带小刀尖圆角半径和小平行面的L槽形;选择细晶粒的非涂层或薄涂层刀片。 硬质合金刀具铣削时如果振动过大,导致工件不牢固的时候,解决方法有:考虑具有正前角槽形的方肩铣刀(90度主偏角);选择具有L槽形的刀片;降低轴向切削力—使用低切深,小刀尖圆角半径和小平行面;选择具有不同齿距的疏齿铣刀。 硬质合金刀具铣削时如果铣削表面质量差,导致铣削每转进给量过大的话,其解决方法有:轴向调整硬质合金刀具或分类刀片,用千分表检查中心高;检查主轴跳动量和硬质合金刀具安装表面;将铣削每转进给量减小到平行锻宽度的70%以内;使用修光刃刀片铣削。更多信息,请访问:http://www.tungsten-carbide.com.cn/Chinese/carbide-cutting-tools.html
发布于
硬质合金刀具
硬质合金刀具铣削介绍
- 星期四, 05 12月 2013 09:53
- 作者 硬质合金产品编辑2
硬质合金刀具铣削是一种非常常见的加工方式,硬质合金刀具铣削是指的是使用可以旋转的多刃刀具切削工件,是一种效率高的加工方法。工作时刀具旋转作主运动,工件移动作进给运动,工件也可以固定,但是此时旋转的硬质合金刀具还需要进行移动,同时完成主运动和进给运动。伴随着机床的不断发展,硬质合金刀具铣削已发展成可加工大量不同结构产品的常用方法。硬质合金铣削刀具的发展也多元化了,而且通过可转位刀片和整体硬质合金技术,还可以提高生产效率、可靠性和质量一致性。更多信息,请访问:硬质合金刀具。 硬质合金刀具铣削加工时需要通过旋转铣刀加工平面、曲面、沟槽、螺纹和齿形,硬质合金切削加工分为车削、铣削、磨削、成形加工和钻削五种。硬质合金刀具铣削具有可间断切削、工件是固定的,通过旋转铣刀进行铣削、铣削中产生的切屑厚度会改变等特点。 硬质合金刀具铣削通常区分为圆周铣削和端铣两大类。圆周铣削用刀片圆周上的刀尖铣削--面铣刀和侧面刃铣刀,也有像立铣刀一样的端面和周身都有切削刃的铣削刀具,能实现两种铣削方式。更多信息,请访问:http://www.tungsten-carbide.com.cn/Chinese/carbide-cutting-tools.html
发布于
硬质合金刀具