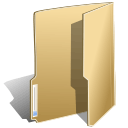
硬质合金刀具 (204)
硬质合金涂层刀具热处理
- 星期三, 04 12月 2013 10:19
- 作者 硬质合金产品编辑2
硬质合金涂层刀具热处理能够吸收一部分的应变能,缓和松弛应力,协调各种相应变状态。硬质合金涂层刀具的热数量由于是在电弧离子镀过程中,基体温度在200~400℃之间,由于温度较低,涂层材料沉积在基体表面骤然冷却,涂层材料由于热膨胀系数的差别有不同的热收缩倾向,从而在涂层各晶粒之间产生热应力。热应力的存在加快了硬质合金涂层刀具在机械切削过程中的失效。钢基CVD-TiN涂层的热处理,涂层经1030℃淬火+250℃回火后,TiN涂层的显微硬度有所提高,涂层的晶体结构更趋于完整,其晶面间距也更接近TiN晶面间距的标准值,同时涂层的致密性有所增加,与基体的结合强度良好。更多信息,请访问:硬质合金刀具。 硬质合金涂层刀具的后处理是在刀具涂层完毕之后采取措施对硬质合金涂层刀具进行相应处理从而增加涂层寿命。但是由于目前对刀具涂层的后处理没有受到重视,有些也只是进行简单的浸油防锈处理。国外对后处理技术研究比较早,但一直持保密态度。硬质合金涂层刀具的后处理工艺包括涂层刀具热处理,深冷处理和磁化处理。三种处理方法虽然有所差别,但是都是为了减小涂层刀具内部的应力并使其重新分布,增强刀刃的抗崩刃能力,从而提高硬质合金涂层刀具的使用寿命。更多信息,请访问:http://www.tungsten-carbide.com.cn/Chinese/carbide-cutting-tools.html
发布于
硬质合金刀具
硬质合金涂层刀具冷处理
- 星期三, 04 12月 2013 10:18
- 作者 硬质合金产品编辑2
硬质合金涂层刀具冷处理增大了刀具的过冷度,从而使得硬质合金中钴的相变自由能差增大,增大了相变驱动力,从而减小刀具在切削过程中的磨料磨损和扩散磨损。在硬质合金涂层刀具中,刀具基体的粘结相Co的成分和性质对硬质合金涂层刀具的强度和变形特性起着至关重要的作用。如果想要改变这种成分和合金的特性,具有两种方法,一种是热处理,另外一种就是对刀具进行冷处理。因为表层的涂层材料的硬度和耐磨性较高,涂层硬质合金允许采用较高的切削速度,从而提高了加工效率;或能在同样的切削速度下大幅度地提高刀具耐用度。更多信息,请访问:硬质合金刀具。 WC的热膨胀系数比Co小3倍多,粘结相是硬质合金涂层到具的主要破坏相,存在于Co相中的很大热应力是不利的因素。深冷处理能够使得WC-Co系硬质合金获得较理想的表面残余应力值。对比YW1硬质合金刀具经过冷处理和未处理的表面残余应力值,结果发现,残余应力值由未处理的4858.665MPa降为4192.297MPa。更多信息,请访问:http://www.tungsten-carbide.com.cn/Chinese/carbide-cutting-tools.html
发布于
硬质合金刀具
硬质合金涂层刀具制备方法
- 星期三, 04 12月 2013 10:17
- 作者 硬质合金产品编辑2
硬质合金涂层刀具的制备方法多种多样,常用的方法有气相沉积、热喷涂、化学热处理、热反应扩散沉积和溶胶凝胶五种。最常用的制备是方法气相沉积,因为制备涂层质量好,己经逐步成为刀具涂层制备方法的主导,气相沉积技术分为化学气相沉积(chemicalvapordeposition,CVD)和物理气相沉积(physicalvapordeposition,PVD)。化学气相沉积(CVD)属于原子沉积类,是利用气态的先驱反应物通过原子、分子间化学反应的途径生成固态涂层的技术。更多信息,请访问:硬质合金刀具。硬质合金涂层刀具的制备方法-气相沉积中的化学气相沉积CVD的过程大多在相对较高的压力和较高的沉积温度环境下进行,因为较高的压力有助于提高涂层的沉积速率,较高的沉积温度可保证化学反应的顺利进行。 硬质合金涂层刀具的化学气相沉积涂层技术不断发展,改进了基体材料和涂层工艺,使用多种和多层涂层材料,出现了第二代、第三代直至第五代、第六代涂层刀具产品。 化学气相沉积涂层工艺温度约为1000℃,结合力可靠,但也带来了一些性能上的缺陷,如刀具切削刃需经过钝化预处理,刀具表面易出现残余拉应力,且不能用于高速钢刀具表面涂层;另外CVD技术的沉积温度太高,超过了许多材料的热处理温度,在这样高的沉积温度下,镀层和硬质合金基体材料都面临着晶粒长大和失碳问题,从而产生一种或几种复式碳化物,即所谓的η相,且通常生成在涂层和基体的界面特别是刃口上。这种η相很脆,降低硬质合金的抗弯强度,同时增大刃口的脆性,从而导致刀刃在使用过程中过早损坏。更多信息,请访问:http://www.tungsten-carbide.com.cn/Chinese/carbide-cutting-tools.html
发布于
硬质合金刀具
硬质合金涂层刀具的切削性能
- 星期三, 04 12月 2013 10:16
- 作者 硬质合金产品编辑2
采用不同材料制作而成的YT15硬质合金涂层刀具的主切削力随切削速度的变化较小,当同切削速度保持相同时,ZrN/Zr硬质合金涂层刀具的主切削力最小。随切削速度的增加呈现先上升后下降的趋势,在速度为178m/min附近达到最大值96N。ZrN硬质合金涂层刀具的主切削力略低于无硬质合金涂层刀具的;ZrN/TiN/Zr硬质合金涂层刀具的主切削力在低速阶段稍高于无硬质合金涂层刀具的,当速度增大到253m/min后,主切削力低于无硬质合金涂层刀具的。不同硬质合金涂层刀具的径向切削力随切削速度的增加呈现上升趋势。更多信息,请访问:硬质合金刀具。 在相同切削速度下,ZrN/Zr硬质合金涂层刀具的径向切削力最小,ZrN硬质合金涂层刀具的径向切削力略低于无硬质合金涂层刀具的,ZrN/TiN/Zr硬质合金涂层刀具的径向切削力略高于无硬质合金涂层刀具的。各刀具轴向切削力随切削速度的变化也不是很大,呈现微增长的趋势,ZrN/Zr硬质合金涂层刀具的轴向切削力最小,其他几种刀具的轴向切削力相差不大。 硬质合金涂层刀具后刀面的磨损量比无硬质合金涂层刀具显著减小。无硬质合金涂层刀具在切削距离超过2000m之后,磨损明显加剧,后刀面磨损量急剧增大,并很快超过0.3mm。ZrN/Zr硬质合金涂层刀具的初期磨损量很小,中期磨损比较均匀,在切削距离为3800m时,后刀面磨损量为0.29mm。ZrN硬质合金涂层刀具的初期磨损量稍大,但中期磨损比较稳定,在切削距离为1800m时,后刀面磨损量为0.23mm,随着切削的进行,当切削距离达到3400m时,后刀面磨损量超过0.3mm。ZrN/TiN/Zr硬质合金涂层刀具的初期磨损量较小,在切削距离为2600m时,后刀面磨损量为0.255mm,后刀面磨损速度加快。从上述比较可得出ZrN/Zr硬质合金涂层刀具的耐磨损性能最好。更多信息,请访问:http://www.tungsten-carbide.com.cn/Chinese/carbide-cutting-tools.html
发布于
硬质合金刀具
ZrN硬质合金涂层刀具性能
- 星期三, 04 12月 2013 10:15
- 作者 硬质合金产品编辑2
ZrN/TiN/Zr、ZrN/Zr和ZrN硬质合金涂层刀具的显微硬度都比基体YT15硬质合金刀片(16.5GPa)还要高,无过渡层的涂层硬度最高,为28.0GPa,复合涂层硬度却略有降低。在基体材料相同的条件下,有锆过渡层的ZrN涂层厚度最大,有锆过渡层的ZrN/TiN复合涂层厚度最小。这是因为在沉积过程中,钛离子和锆离子相互碰撞,导致沉积速度降低,所以,在相同的沉积时间内,涂层厚度最小。无过渡层的涂层的界面结合力低于有过渡层涂层的,ZrN/TiN/Zr涂层的结合力最高,无过渡层的ZrN涂层的结合力最低。这是由于过渡层锆和复合涂层TiN与YT15基体和ZrN涂层之间发生离子扩散,减小了涂层与基体之间的残余热应力,从而提高了涂层的结合力。更多信息,请访问:硬质合金刀具。硬质合金涂层刀具涂层的硬度和厚度对刀具的耐磨性起着很大的影响,其硬度越高,耐磨性相对也越高。但是硬度高了,涂层的裂纹敏感度也增大。涂层过薄,不能保护基体材料,耐磨性相对差些;涂层太厚,因涂层与基体材料间的热膨胀系数的差别而产生的残余应力就大,过大的残余应力会导致裂纹产生,从而使材料的强度降低。因此,涂层厚度应适宜。涂层的界面结合力大表明涂层与刀具材料的匹配度好,结合强度也大,刀具的使用寿命长。刀具材料与涂层材料匹配度越好,其热膨胀系数越接近,刀具就会有高的导热性能和耐热性。更多信息,请访问:http://www.tungsten-carbide.com.cn/Chinese/carbide-cutting-tools.html
发布于
硬质合金刀具
ZrN硬质合金涂层刀具
- 星期三, 04 12月 2013 10:13
- 作者 硬质合金产品编辑2
ZrN硬质合金涂层刀具除具有耐腐蚀、耐高温、耐磨损性能之外,还具有良好的力学性能和导电性能,美观的金黄色外表等优点。ZrN涂层已广泛应用于电子电路中的电接触层、珠宝业中的装饰层和机械摩擦中的减摩层等,但在刀具涂层的应用还不常见。随着制造技术的进步,机械加工不断向高精化、高速化方向发展,因此对切削刀具在强度、耐高温、耐磨损和使用寿命等方面的性能要求也不断提高。对刀具进行涂层处理是提高刀具性能的重要手段之一。由于涂层处理可以提高加工效率和精度、延长刀具使用寿命、降低加工成本,因此,硬质合金涂层刀具在金属切削加工中的应用越来越广泛。更多信息,请访问:硬质合金刀具。 常用硬质合金涂层刀具的涂层材料有碳化物、氮化物、氧化物、硼化物和硫化物等,近年来还发展了聚晶金刚石、立方氮化硼等。涂层结构也已由最初的TiC和TiN单涂层发展到复合多涂层,如TiC/TiCN/TiN、TiC/Al2O3和TiC/Al2O3/TiN等复合涂层。TiC和TiN单涂层制备简单,但在应用中也逐渐暴露了一些问题,如耐蚀性差、高温硬度低等。 采用中频磁控溅射和电弧离子镀相结合的多功能PVD涂层制备方法有利于得到较高致密度、较好附着强度、耐久性强的硬质合金涂层刀具,具有离化率高及沉积速度快等优点,已在生产中得到广泛的应用。为了提高刀具的性能,在某些应用方面取代TiC和TiN硬质合金涂层刀具,作者采用中频磁控溅射和电弧离子镀相结合的方法,在最常用的、与ZrN最匹配的硬质合金上制备ZrN单涂层和复合ZrN涂层,并通过切削试验研究了硬质合金涂层刀具的切削性能。更多信息,请访问:http://www.tungsten-carbide.com.cn/Chinese/carbide-cutting-tools.html。
发布于
硬质合金刀具
YG6X-1硬质合金刀头
- 星期二, 03 12月 2013 08:17
- 作者 硬质合金产品编辑4
YG6X-1硬质合金刀头,相当于ISO分组代号中的K20,其密度为14.6~15.0g/cm³,抗弯强度不小于1500N/MM²,硬度不小于90HRA。由于其良好的性能,因此YG6X-1硬质合金适于铸铁,有色金属及其合金非金属材料连续切削时的精车,间断切削时的半精车、精车、小断面精车、粗车螺纹、连续断面的半精铣与精铣,孔的粗扩与精扩。在将碳化钨粉与金属结合剂一起进行混合碾磨以生产某种牌号硬质合金粉料时,可以采用各种不同的组合方式。最常用的钴含量为3%-25%(重量比),而在需要增强刀具抗腐蚀性的情况下,则需要加入镍和铬。 更多信息,请见:http://3g.chinatungsten.com/zwmobi.php?zwmobi=view&V=21&mid=394&cid=1446。 减小碳化钨颗粒的尺寸可以提高材料的硬度,但在烧结工艺中,碳化钨的粒度必须保持不变。烧结时,碳化钨颗粒通过溶解再析出的过程结合和长大。在实际烧结过程中,为了形成一种完全密实的材料,金属结合剂要变成液态(称为液相烧结)。通过添加其他过渡金属碳化物,包括碳化钒(VC)、碳化铬(Cr3C2)、碳化钛(TiC)、碳化钽(TaC)和碳化铌(NbC),可以控制碳化钨颗粒的长大速度。这些金属碳化物通常是在将碳化钨粉与金属结合剂一起进行混合碾磨时加入,尽管碳化钒和碳化铬也可以在对碳化钨粉进行渗碳时形成。更多信息,请访问:硬质合金刀头。
发布于
硬质合金刀具
YG8N硬质合金刀头
- 星期二, 03 12月 2013 08:14
- 作者 硬质合金产品编辑4
YG8N硬质合金刀头,相当于ISO分组代号中的K30,其密度为14.5~14.8g/cm³,抗弯强度不小于2000N/MM²,硬度不小于90HRA。由于其良好的性能,因此YG8N硬质合金加工冷硬合金铸铁与耐热合金钢可获得良好的效果,也适于普通铸铁的精加工。在许多情况下,成品工件需要进行涂层。涂层能够提供润滑性和增加硬度,还能为基体提供扩散屏障,使其暴露于高温下时可防止氧化。硬质合金基体对于涂层的性能至关重要。除了定制基体粉料的主要特性以外,还可以通过化学选择和改变烧结方法定制基体的表面特性。 更多信息,请见:http://3g.chinatungsten.com/zwmobi.php?zwmobi=view&V=21&mid=394&cid=1446。 利用回收的废旧硬质合金材料也可以生产牌号碳化钨粉料。废旧硬质合金的回收和再利用在硬质合金行业已有很长历史,是该行业整个经济链的一个重要组成部分,它有助于降低材料成本、节约自然资源和避免对废弃材料进行无害化处置。废旧硬质合金一般可通过APT(仲钨酸铵)工艺、锌回收工艺或通过粉碎后进行再利用。这些“再生”碳化钨粉通常具有更好的、可预测的致密性,因为其表面积比直接通过钨渗碳工艺制成的碳化钨粉更小。更多信息,请访问:硬质合金刀头。
发布于
硬质合金刀具
YG8硬质合金刀头,相当于ISO分组代号中的K30,其密度为14.5~14.9g/cm³,抗弯强度不小于1600N/MM²,硬度不小于89.5HRA。由于其良好的性能,因此YG8硬质合金适于铸铁、有色金属及其合金与非金属材料加工中,不平整断面和间断切削时的粗车、粗刨、粗铣,一般孔和深孔的钻孔、扩孔。刀具制造商基于自己的制造工艺(如脱蜡方法、加热速度、烧结时间、温度和渗碳电压),可能会对使用的牌号硬质合金粉料提出一些特殊要求。有些刀具制造商可能是在真空炉中烧结工件,而另一些刀具制造商则可能使用热等静压(HIP)烧结炉(它是在工艺循环临近结束时才对工件加压,以消除任何残留孔隙)。 更多信息,请见:http://3g.chinatungsten.com/zwmobi.php?zwmobi=view&V=21&mid=394&cid=1446。 不同种类的碳化钨粉、混合料成分和金属结合剂含量、晶粒长大抑制剂的类型和用量等的组合变化,构成了形形色色的硬质合金牌号。这些参数将决定硬质合金的显微结构及其特性。某些特定的性能组合已成为一些特定加工用途的首选,从而使对多种硬质合金牌号进行分类具有了意义。两种最常用的、面向加工用途的硬质合金分类体系分别为C牌号体系和ISO牌号体系。尽管这两种体系都不能完全反映影响硬质合金牌号选择的材料特性,但它们提供了一个探讨的起点。对于每种分类法,许多制造商都有它们自己的特殊牌号,由此产生了形形色色、五花八门的各种硬质合金牌号。更多信息,请访问:硬质合金刀头。
发布于
硬质合金刀具
YG10X硬质合金刀头
- 星期二, 03 12月 2013 08:06
- 作者 硬质合金产品编辑4
YG10X硬质合金刀头,相当于ISO分组代号中的K35,其密度为14.3~14.7g/cm³,抗弯强度不小于2200N/MM²,硬度不小于89.5HRA。由于其良好的性能,因此YG10X硬质合金适于制造细径微钻、立铣刀、旋转锉刀等。硬质合金是由硬度和熔点都很高的碳化物,用Co、Mo、Ni作粘结剂烧结而成的粉末冶金制品。YG10X硬质合金刀头常温硬度可达78~82 HRC,能耐850~1000℃的高温,切削速度可比高速钢高4~10倍。但其冲击韧性与抗弯强度远比高速钢差,因此很少做成整体式刀具。实际使用中,常将硬质合金刀片焊接或用机械夹固的方式固定在刀体上。更多信息,请见:http://3g.chinatungsten.com/zwmobi.php?zwmobi=view&V=21&mid=394&cid=1446。 碳化钨/钴(WC/Co):首先进行商业应用的烧结硬质合金是由碳化钨高角颗粒与金属钴粘结而成。最初打算用于拔丝模,这个成分类型仍然被视为对简单磨损具有极好的抵抗力,因此也广泛应用于切削加工之中。对于从装填密度而获得的最大硬度,碳化钨细粒应尽可能的小,最好低于1μm(0.00004英寸)而且对于特殊用途要相当小。随着钴含量的降低其硬度和耐 磨损性能增高,只要保证烧结中存在最低含量的钴(2%即可,尽管实际的最低含量是3%)即可。总之,随着碳化物细粒或钴的含量或者两者的增加--通常是一 致的--会获得更硬或者较软的等级。不能见到气孔,甚至在最高的光学放大下也不应看到。 YG10X硬质合金刀头所用WC/Co的成分范围大约是2%-13%的钴,而且其细粒尺寸从小于0.5到大于5μm(0.00002-0.0002英寸)。对于冲压工 具,冷锻模和其他适用于中等或严重振动零部件的制品应用,钴的成分可高达30%,而且细粒尺寸最大可达10μm(0.0004英寸)。近年来发现将亚微米 (小于0.00004英寸)碳化物细粒和相对较高的钴成分组合起来的“微细粒”碳化物增加了在低速加工和高速率加工下的使用。更多信息,请访问:硬质合金刀头。
发布于
硬质合金刀具